Recognizing What is Porosity in Welding: Causes and Solutions
The Scientific Research Behind Porosity: A Comprehensive Guide for Welders and Fabricators
Understanding the elaborate mechanisms behind porosity in welding is critical for welders and makers pursuing impeccable craftsmanship. As metalworkers explore the depths of this sensation, they uncover a world governed by different variables that influence the formation of these tiny gaps within welds. From the structure of the base products to the complexities of the welding process itself, a wide variety of variables conspire to either exacerbate or minimize the presence of porosity. In this thorough guide, we will unravel the science behind porosity, discovering its effects on weld quality and introduction advanced methods for its control. Join us on this journey through the microcosm of welding flaws, where accuracy fulfills understanding in the quest of perfect welds.
Comprehending Porosity in Welding
FIRST SENTENCE:
Evaluation of porosity in welding discloses crucial insights right into the integrity and high quality of the weld joint. Porosity, defined by the presence of tooth cavities or spaces within the weld steel, is a common issue in welding processes. These gaps, otherwise appropriately dealt with, can compromise the structural integrity and mechanical buildings of the weld, bring about prospective failings in the completed item.
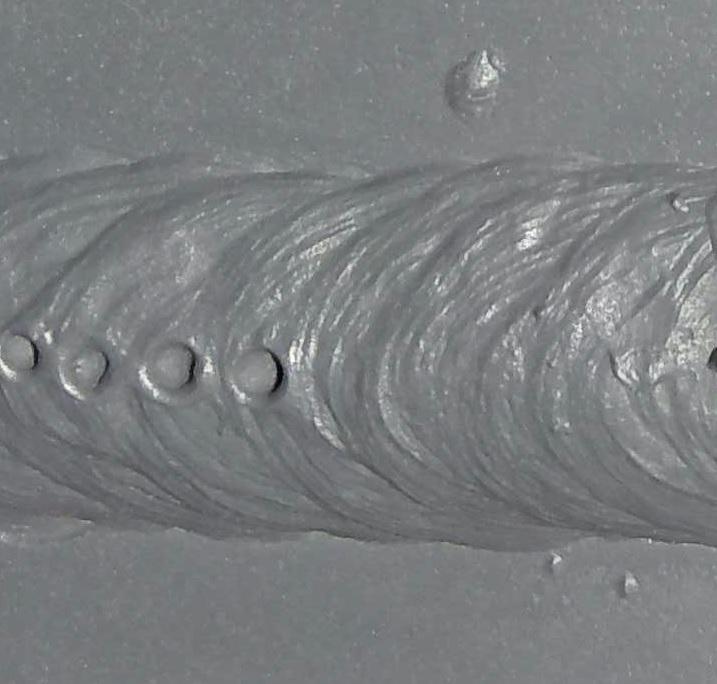
To discover and quantify porosity, non-destructive testing techniques such as ultrasonic testing or X-ray evaluation are often used. These techniques permit the recognition of internal issues without endangering the honesty of the weld. By examining the size, shape, and distribution of porosity within a weld, welders can make educated choices to improve their welding processes and achieve sounder weld joints.
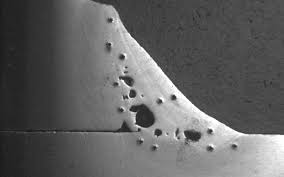
Elements Influencing Porosity Formation
The occurrence of porosity in welding is influenced by a myriad of aspects, ranging from gas shielding effectiveness to the intricacies of welding specification settings. One vital variable adding to porosity formation is insufficient gas shielding. When the protecting gas, commonly argon or carbon dioxide, is not efficiently covering the weld pool, atmospheric gases like oxygen and nitrogen can contaminate the molten metal, leading to porosity. Additionally, the sanitation of the base products plays a considerable function. Impurities such as corrosion, oil, or dampness can evaporate during welding, creating gas pockets within the weld. Welding parameters, consisting of voltage, present, travel speed, and electrode type, additionally influence porosity development. Using improper setups can produce extreme spatter or warmth input, which subsequently can cause porosity. Furthermore, the welding strategy employed, such as gas metal arc welding (GMAW) or protected metal arc welding view it (SMAW), can influence porosity development as a result of variations in important source warmth circulation and gas coverage. Understanding and managing these variables are essential for decreasing porosity in welding procedures.
Results of Porosity on Weld Quality
The existence of porosity likewise deteriorates the weld's resistance to corrosion, as the entraped air or gases within the voids can respond with the surrounding environment, leading to destruction over time. Additionally, porosity can prevent the weld's capacity to withstand pressure or effect, further threatening the overall high quality and dependability of the bonded framework. In important applications such as aerospace, auto, or structural constructions, where safety and security and durability are paramount, the harmful effects of porosity on weld quality can have extreme consequences, stressing the significance of decreasing porosity with appropriate welding techniques and procedures.
Techniques to Minimize Porosity
Furthermore, making use of the appropriate welding parameters, such as the right voltage, existing, and take a trip speed, is vital in protecting against porosity. Maintaining a constant arc length and angle throughout welding additionally helps minimize the probability of porosity.

Making use of the ideal welding method, such as back-stepping or employing a weaving motion, can additionally assist distribute warmth uniformly and lower the opportunities of porosity formation. By implementing these strategies, welders can successfully reduce porosity and produce high-quality welded joints.

Advanced Solutions for Porosity Control
Executing advanced modern technologies and innovative approaches plays a pivotal function in attaining exceptional control over porosity in welding procedures. Additionally, using advanced welding methods such as pulsed MIG welding or changed atmosphere welding can likewise aid mitigate porosity link problems.
An additional innovative service includes the usage of advanced welding devices. Making use of equipment with built-in attributes like waveform control and innovative power sources can boost weld quality and reduce porosity risks. The implementation of automated welding systems with precise control over parameters can considerably lessen porosity issues.
In addition, incorporating innovative surveillance and inspection modern technologies such as real-time X-ray imaging or automated ultrasonic screening can assist in identifying porosity early in the welding process, permitting prompt rehabilitative activities. Generally, incorporating these sophisticated services can substantially boost porosity control and boost the general high quality of welded components.
Verdict
In verdict, understanding the scientific research behind porosity in welding is vital for welders and fabricators to create top quality welds - What is Porosity. Advanced remedies for porosity control can additionally boost the welding process and make certain a strong and reputable weld.